汽车覆盖件冲压全场应变检测步骤和流程
板料成形过程中的变形较为复杂,包含弹性变形、塑性变形、弹塑性变形等。其中,塑性变形会使得钣金件内部材料发生流动,从而造成钣金件厚度分布不一致,并且会产生应力集中。在厚度变薄的区域及应力集中的区域,产生破裂的概率就会加大,因而最终影响钣金零件的使用寿命等(成形性能受到影响)。为此,在钣金零件成形后,都需要对其表面的厚度及应力集中等进行测量。应力是指单位面积上力的大小,由于钣金件在成形过程中,表面某一点处力的大小很难直接测量得到(大部分钣金零件都是经冲压成形),所以无法直接测量得到钣金件表面的应力分布。
在工程实际中,是通过测量钣金件表面的应变而间接获得应力场,因为根据广义胡克定律,对于给定的材料,其应力应变曲线是唯一的,也就是说每一个应变值都对应唯一的应力值,反之亦然。因此,可以通过测量钣金件表面的应变来测量钣金件表面的应力,而钣金件表面应变值的测量要容易的多。网格分析法是一种简单、高效的测量钣金件表面应变的方法,其测量流程包括:网格制备、网格尺寸测量、应变计算。其中网格制备及应变计算都比较成熟,关键之处在于网格尺寸的测量。
(1) 测量对象
实验中,制件材料为不锈钢304,材料厚度为0.7mm。网板大小为:500mm×250mm,网格节点间距为2mm,整个网板包含节点数目大概为31000左右。制备一个网板大小的网格所需时间大概为2分钟左右。该打标机适合于制备尺寸比较大的试件。打印的图案比较清晰,即使成形后也易于识别。在板料上制备好网格以后,进行冲压成形试验。
图 7 23冲压成形制件
(2) 测量过程
由于被测量试件尺寸比较大,总共制备了14块与网板大小一致的网格。因此需要多次测量,然后将多次测量结果拼合起来。在本例中,总共测量了14次,每次测量一个网板大小的网格,测量过程中保证相邻的网格之间有公共编码标志点,用来将14个网格的坐标归一。如图 7 24所示,第二块网格与第一块网格之间设置了公共的拼接点,这样单块网格计算完成后,可以通过公共拼接点将坐标系统一起来。
图 7 24分块拼接
具体测量过程如下:
第一步,测量第一块网格,在待测量区域周围放置一些编码标志点及比例尺,然后用数码相机,按照6.3.2节所讲述的方法从不同的站位拍摄了30张像片,如图 7 25所示。这些数据是后期计算的原始数据。
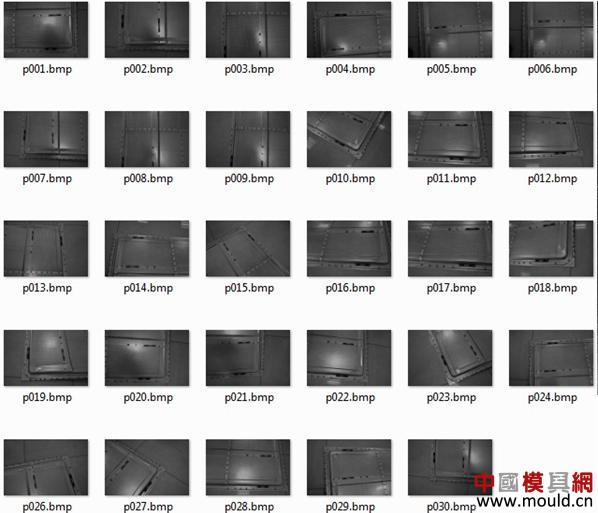
图 7 25冲压实验拍摄的像片(第一块网格)
第二步,将采集的像片导入XJTUSM系统软件中,进行图像的识别。紧接着,对这些图像进行定向、匹配、重建、捆绑调整等操作,计算得到网格节点的三维坐标,如图 7 26所示。表 7 7显示了部分非编码点的三维坐标,其中非编码点的标号(ID值)是软件自动给分配的。
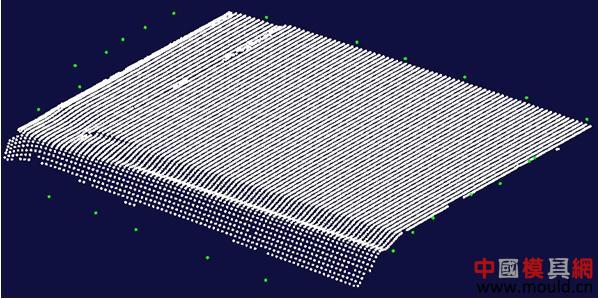
图 7 26计算得到点阵网格节点三维坐标
第三步,网格连接,按照6.3.4节网格连接的原理,将相邻的4个网格节点依次连接起来形成四边形网格,如图 7 27所示。
图 7 27连接相邻网格节点形成四边形网格
第四步,应变计算,根据同一网格在变形前后网格尺寸的变化,套用应变计算公式计算出网格节点的各种应变值及表面厚度减薄率等(图 7 28)。
图 7 28最大主应变计算结果(工程应变)
第五步,测量第二块网格,保留用于拼接用的公共编码标志点,将比例尺及多余的编码标志点放置在第二块网格周围,然后用数码相机,按照6.3.2节所讲述的方法从不同的站位拍摄了40张像片,如图 7 29所示。
图 7 29冲压实验拍摄的像片(第二块网格)
第六步,将采集的第二块网格像片导入XJTUSM系统软件中,进行图像的识别。紧接着,对这些图像进行定向,计算得到网格编码标志点的三维坐标,然后指定公共编码标志点(图 7 30),将第二块拼接至第一个块,如图 7 31所示。
图 7 30拼接对话框
图 7 31第二块网格编码标志点拼接至第一块网格
第七步,重建拼接后的第二块网格。并计算应变(图 7 32)。
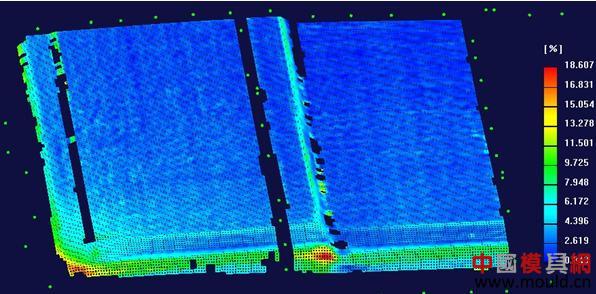
图 7 32第二块网格最大主应变
第八步, 重复第五-七步,直至所有网格测量完毕。
(3) 测量结果分析
图 7 33、图 7 34、图 7 35、图 7 36分别是钣金件表面得到的最大主应变、最小主应变、厚度减薄率、成形极限曲线图(FLD)。通过应变值及厚度应变分布色温图可以直观地看出危险区域的具体位置,结合FLC曲线,则可以判定材料的性能是否满足冲压的要求,可以指导冲压工艺流程的调整、模具的调试等,从而缩短新产品开发的周期。表 7 8显示了部分网格节点的三维坐标及对应的应变值。该实例再一次说明了本文方法的有效性。
图 7 33最大主应变
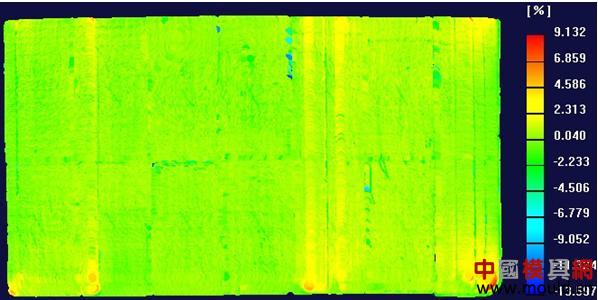
图 7 34最小主应变
图 7 35厚度减薄率
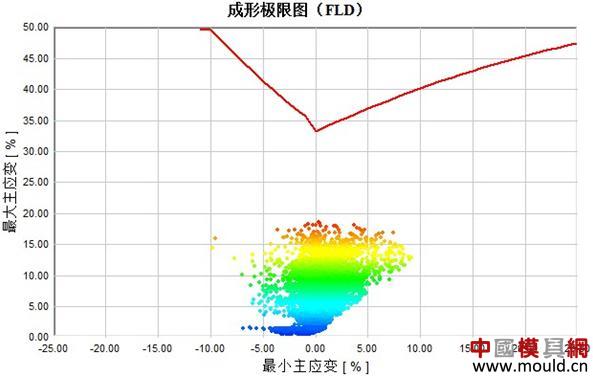
图 7 36成形极限曲线图(FLD)